Mastering the Art of Plastic Mould Manufacture
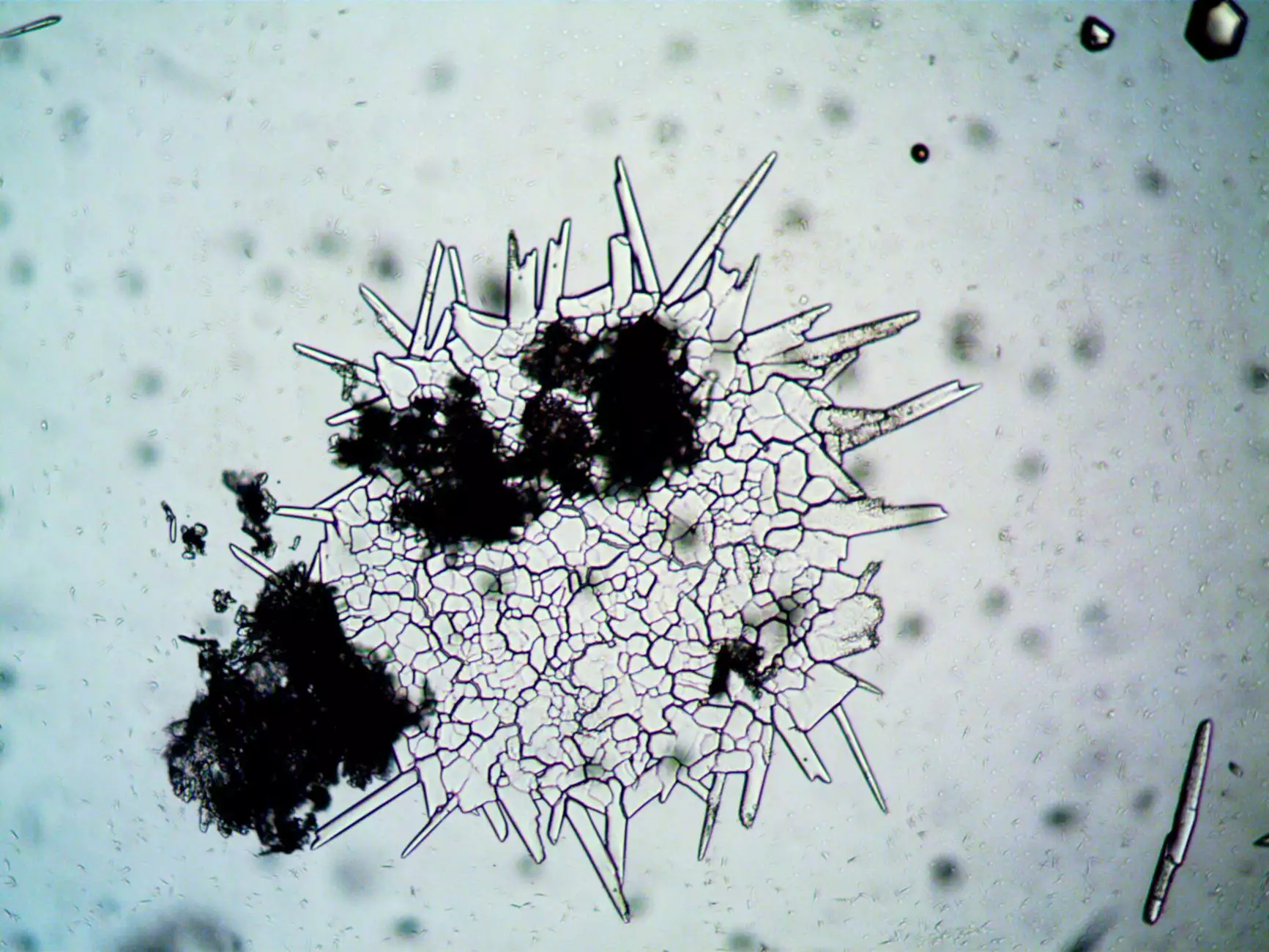
Plastic mould manufacture is a critical component of modern manufacturing that is often overlooked but plays a pivotal role in various industries. Understanding the dynamics of this field can equip businesses with the tools to innovate and maintain competitive edges. This article aims to delve deep into the intricacies of plastic mould making, the essential roles of plastic injection mould manufacturers, and how to achieve exceptional quality in mould design and production.
The Importance of Plastic Mould Manufacture
The plastic mould manufacture process is at the heart of numerous industries ranging from automotive and electronics to consumer goods and healthcare. This process allows for:
- High-volume production: Moulded plastics can be produced in high volumes efficiently, making them ideal for mass production.
- Cost-effectiveness: With increased production volume comes reduced costs per unit, allowing companies to optimize their operations.
- Design flexibility: Plastics can be moulded into complex shapes that are often impossible with traditional materials like metal.
- Weight reduction: Plastic components can significantly reduce the weight of products, particularly in automotive and aerospace sectors.
Understanding the Process of Plastic Mould Manufacture
1. Design Phase
The first step in plastic mould manufacture is designing the mould. This involves generating a 3D model using advanced computer-aided design (CAD) software. Key considerations include:
- Material selection based on chemical compatibility and physical requirements.
- Designing for manufacturability to minimize production challenges.
- Optimizing the mould cooling systems to enhance cycle times and product quality.
2. Material Selection
Choosing the right material is vital. Common materials used in plastic mould manufacture include:
- Steel: Known for its durability, it's often used for high-volume dies and complex moulding tasks.
- Aluminium: Lightweight and easy to machine, ideal for short runs and prototype moulds.
- Titanium: Exceptional strength and resistance to corrosion, but often more costly.
3. Mould Fabrication
Once the design is set and materials are selected, the fabrication process begins. This may include:
- CNC Machining: Precise machining of mould components using computer-controlled equipment.
- EDM (Electrical Discharge Machining): Ideal for creating complex geometries and achieving high tolerance specifications.
- 3D Printing: Recently gaining traction for rapid prototyping of mould components before the final manufacturing.
4. Testing and Quality Control
Quality assurance is paramount. Each mould must undergo rigorous testing to ensure:
- Dimensional accuracy.
- Surface finish quality.
- Functional performance and durability under expected operating conditions.
Types of Plastic Moulds
There are several types of moulds available in the plastic mould manufacture sector, each serving specific purposes:
Casting Moulds
Casting moulds are typically used for low-volume production of parts. These are cost-effective for producing complex shapes.
Injection Moulds
Injection moulds are widely used in high-volume production due to their ability to create large numbers of identical parts quickly. The process involves:
- Heating plastic granules until melted, followed by injecting them into a mould cavity under pressure.
- Cooling the mould to solidify the plastic before removing the finished product.
Blow Moulds
Blow moulds are used primarily for creating hollow products such as bottles. The process involves:
- Creating a parison that is then inflated until it takes the shape of the mould.
Plastic Mould Makers: The Unsung Heroes
Plastic mould makers are skilled artisans who translate design visions into reality. Their expertise in various aspects of mould design and fabrication is crucial. Important characteristics of successful plastic mould makers include:
- Technical proficiency: Skilled in computer-aided design (CAD) and manufacturing processes.
- Creativity: Ability to devise innovative solutions for complex design challenges.
- Attention to detail: Ensuring that every aspect of the mould meets stringent specifications.
The Role of Plastic Injection Mould Manufacturers
The role of plastic injection mould manufacturers extends beyond simply creating moulds. They control the entire lifecycle, which includes:
- Consulting with clients to understand product needs and specifications.
- Prototyping to refine product designs before mass production.
- Managing production runs, including quality checks and adjustments throughout the manufacturing process.
Challenges in Plastic Mould Manufacture
The field is not without challenges. Key issues facing plastic mould manufacturers include:
- Cost pressures: With increasing competition, maintaining profitability can be difficult.
- Technological advancements: Keeping pace with rapid changes in technology and methodologies.
- Sustainability: Growing demands for eco-friendly materials and processes necessitate innovation in practices and materials.
Future Trends in Plastic Mould Manufacture
The future of plastic mould manufacture looks promising, with several trends shaping its trajectory:
- Automation: Enhanced efficiency through the use of robotic systems and automated quality checks.
- 3D Printing: Integration of additive manufacturing into mould making to reduce lead times and costs.
- Material Innovation: Exploring alternatives like bio-based plastics and advanced composites.
Conclusion
In conclusion, plastic mould manufacture serves as a backbone for various industries by transforming raw materials into high-performance products. As businesses seek to innovate, investing in high-quality mould design and manufacturing becomes essential. Whether it’s through embracing new technologies, focusing on sustainability, or enhancing production efficiency, the future of mould manufacture is rich with opportunities. By prioritizing quality and adaptability, companies like hanking-mould.com position themselves at the forefront of this ever-evolving industry.