Lathe Turning Parts Suppliers: Driving Innovation in Metal Fabrication
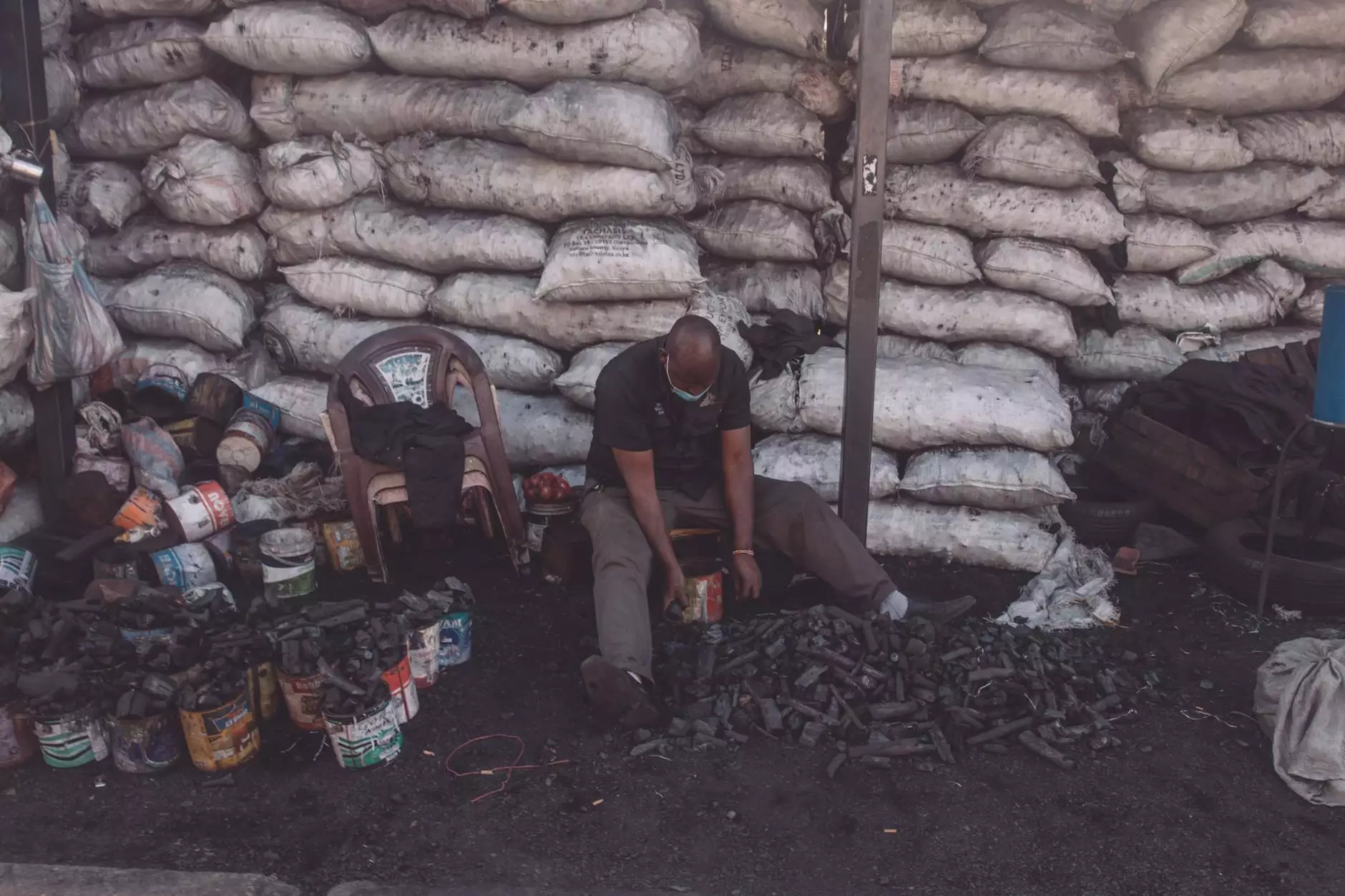
In the ever-evolving world of metal fabrication, the role of lathe turning parts suppliers cannot be overstated. These suppliers are pivotal in facilitating precision machining, ensuring the consistent production of top-quality components essential for numerous industries. This article delves into the significance of lathe turning parts suppliers, their impact on metal fabrication, and how businesses can harness their expertise to enhance operational efficiency and product quality.
Understanding Lathe Turning and Its Importance
Lathe turning is a machining process that removes material from a fixed workpiece to shape it into desired forms. It is a fundamental method used in manufacturing cylindrical parts with high precision. The importance of lathe turning in the production of metal parts lies in its ability to create intricate designs and precise dimensions that many other machining processes cannot achieve. This makes it indispensable for industries such as:
- Aerospace
- Automotive
- Electronics
- Medical devices
- Machinery
What Are Lathe Turning Parts?
Lathe turning parts refer to components produced using the lathe machining process. These parts can include:
- Shafts
- Spindles
- Bushings
- Bolts and screws
- Gears
Each of these components plays a vital role in assembling larger machines and systems, contributing to the overall functionality and performance of the end products.
Qualities to Look for in Lathe Turning Parts Suppliers
Choosing the right lathe turning parts supplier is crucial for businesses engaged in metal fabrication. Here are some key qualities that should guide your selection process:
1. Experience and Expertise
A supplier with extensive experience in lathe turning will have a deep understanding of the intricacies involved in precision machining. Their expertise ensures that your parts meet the required specifications and quality standards.
2. Quality Assurance
Look for suppliers that adhere to strict quality control measures. This can include certifications like ISO 9001, which indicate a commitment to maintaining high manufacturing standards and meeting customer expectations.
3. Range of Services
Many lathe turning parts suppliers offer additional services that can be beneficial to your operations. These may include:
- Custom engineering services
- Rapid prototyping
- Inventory management solutions
Choosing a supplier that provides a comprehensive suite of services can enhance your supply chain efficiency.
4. Technological Capability
Modern lathe turning requires advanced machinery and technology to ensure precision and efficiency. Supplier facilities equipped with the latest CNC lathes and software can significantly improve production quality and output rates.
5. Customer Support
A responsive customer support team is essential for addressing any issues that may arise during the production process. Suppliers who prioritize customer service help build long-term partnerships and mitigate production disruptions.
The Impact of Lathe Turning Parts Suppliers on Metal Fabrication
Lathe turning parts suppliers play a vital role in the metal fabrication industry by providing components that are critical for various manufacturing processes. Their contributions can be observed in several ways:
1. Enhanced Precision
Precision is key in any manufacturing process. Suppliers specializing in lathe turning can produce components with extremely tight tolerances, which is essential for high-quality end products. This capability helps businesses produce machinery and devices that function seamlessly.
2. Reducing Production Time
With access to advanced machinery and technologies, lathe turning parts suppliers can significantly reduce production time. This efficiency not only speeds up the manufacturing process but also enables businesses to respond faster to market demands, giving them a competitive edge.
3. Innovation in Design
Lathe turning parts suppliers often collaborate with customers to develop innovative designs that utilize the unique capabilities of lathe machining. This collaborative approach fosters creativity and allows businesses to experiment with new ideas and product designs.
4. Cost Efficiency
By sourcing high-quality parts from reliable suppliers, businesses can reduce waste and minimize rework due to flaws in components. This leads to lower overall manufacturing costs and greater profitability.
5. Supply Chain Reliability
Partnering with reputable lathe turning parts suppliers helps ensure a steady supply of essential components. This reliability is crucial for maintaining production schedules and minimizing downtime.
Building Relationships with Lathe Turning Parts Suppliers
Establishing strong partnerships with lathe turning parts suppliers is beneficial for both parties. Here are some strategies for nurturing these relationships:
1. Communication is Key
Maintain open lines of communication with your suppliers. Regular updates on your production needs and any changes in demand can help suppliers adjust their services accordingly.
2. Provide Feedback
Offering constructive feedback on the quality of parts and service reinforces mutual trust. Suppliers appreciate knowing how they can better meet your needs, leading to improved collaboration.
3. Foster Transparency
Being transparent about your production processes and requirements encourages suppliers to align their operations with your business goals. This openness can foster a more productive partnership.
Future Trends in Lathe Turning and Metal Fabrication
The world of metal fabrication is rapidly changing, with new technologies shaping how lathe turning and other processes are performed. Here are some future trends to watch:
1. Automation and Robotics
The integration of automation and robotics in lathe turning processes will dramatically improve efficiency and precision. Automated systems can operate continuously, minimizing human error and maximizing productivity.
2. Advanced Materials
As new materials emerge, lathe turning parts suppliers will need to adapt their processes to work with these innovations. This adaptability will be crucial for supporting industries that require advanced materials for improved performance.
3. Sustainability Initiatives
There is a growing emphasis on sustainability in manufacturing. Suppliers are likely to increasingly focus on eco-friendly practices, such as recycling materials and reducing waste during the production of lathe turning parts.
4. Digital Technologies
The use of digital technologies like 3D modeling and simulation software will continue to enhance design processes. This allows suppliers to create virtual prototypes, reducing the time and cost associated with physical prototyping.
Conclusion
In conclusion, the role of lathe turning parts suppliers is integral to the success of businesses within the metal fabrication industry. By choosing the right suppliers and fostering strong partnerships, companies can enhance their production efficiency, maintain high-quality standards, and innovate within their respective fields. As the industry continues to evolve with new technologies and trends, staying informed and adaptable will be crucial for both suppliers and manufacturers alike.
For businesses seeking top-notch metal fabrication solutions, collaborating with renowned suppliers like Deep Mould is an excellent way to ensure access to superior lathe turning parts and, thereby, bolster their operational capabilities.